Knitted fabric production process
As a Chinese fabric factory focusing on knitted fabrics and bonded fabrics, Shaoxing Starke is committed to providing customers with high-quality fabric solutions. Today, we will take you to have an in-depth understanding of our fabric production process, covering every aspect from yarn production to finished product processing. Our process consists of five main steps: yarn production, weaving, dyeing, finishing and finished product processing. Through this series of fine processes, we ensure that every meter of fabric can meet our customers' needs and expectations. Let’s explore this journey full of creativity and technology together!
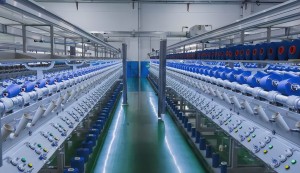
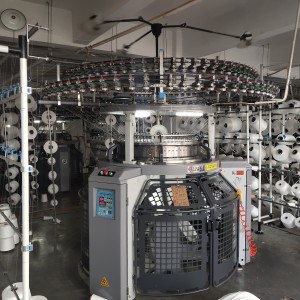
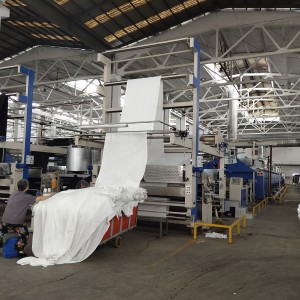
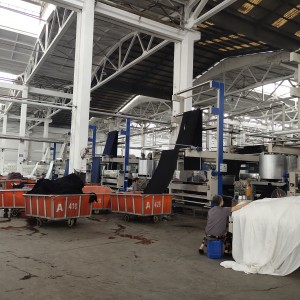
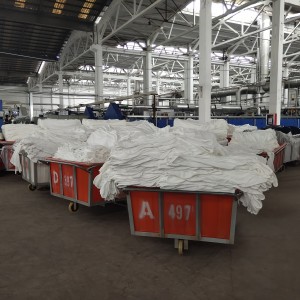
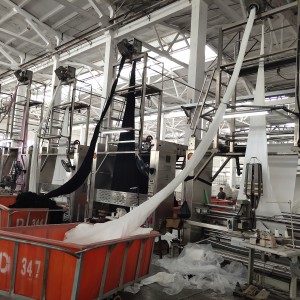
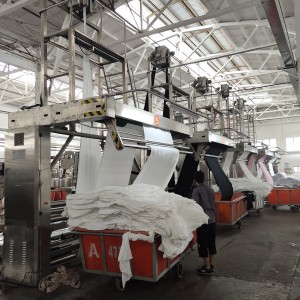
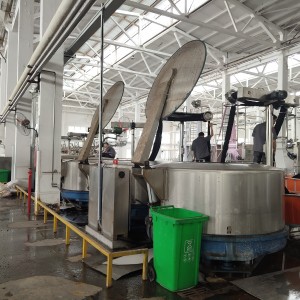
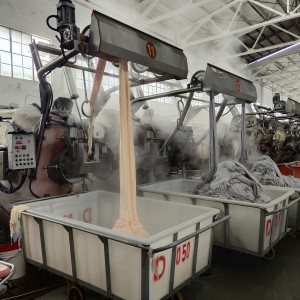
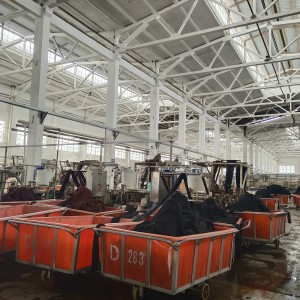
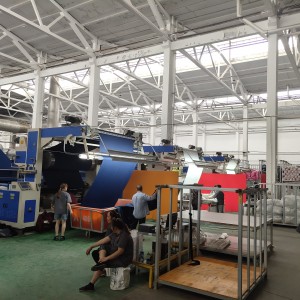
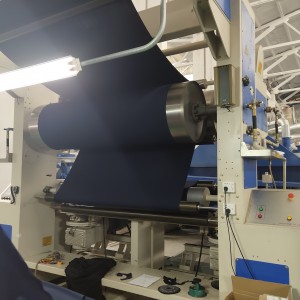
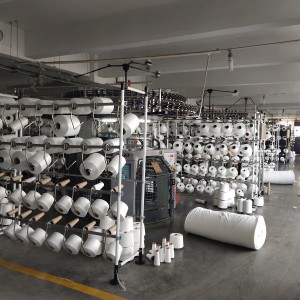
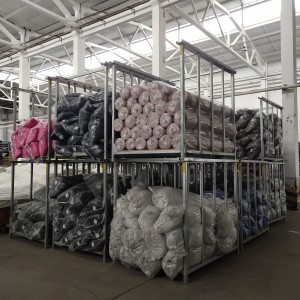
1.Produce yarn
The first step in making knitted fabrics is the production of yarns, which is a crucial process because the quality of knitted fabrics directly depends on the yarns used. The raw materials of knitted fabrics are mainly yarns, which are usually made of a variety of materials such as pure cotton, polyester, wool, silk, etc., and are blended in appropriate proportions to achieve the ideal feel and performance. For example, pure cotton yarn has good breathability and comfort, while polyester provides stronger wear resistance and wrinkle resistance, wool can increase warmth, and silk gives the fabric a glossy and smooth feel. Therefore, choosing the right raw materials and blending ratios is the key to making high-quality knitted fabrics.
In the production process of yarn, quality control is particularly important because the quality of yarn directly affects the quality and performance of the final product. In order to ensure the excellent quality of yarn, the production process needs to go through a series of delicate processes. These processes include cotton selection, opening, drawing, combing, roving and spun yarn, etc.
First, cotton selection is to select high-quality cotton fibers from a large amount of cotton, remove impurities and inferior cotton to ensure the purity of the raw materials. Next, the opening process uses mechanical equipment to open the cotton fibers and make them loose for subsequent processing. Then, in the drawing process, multiple cotton yarns are combined to form a uniform yarn strip to improve the uniformity and strength of the yarn.
The combing process uses special combing equipment to remove short fibers and impurities in the yarn strip to further improve the smoothness and strength of the yarn. After combing, the yarn is usually more delicate and suitable for making high-end knitted fabrics. Subsequently, the production of roving and spun yarn is to spin the combed yarn strips to form yarns of different thicknesses to meet the needs of different knitted fabrics.
2.Fabric Weaving
After the yarn production is completed, the next step is the fabric weaving, which is a crucial step in the entire production process. Knitting technology, as the core link of knitted fabric production, involves many aspects, including the number of knitting needles, knitting machine models, knitting methods, etc. These factors not only affect production efficiency, but are also directly related to the quality, appearance and feel of the final product.
First, the choice of knitting needles will affect the density and thickness of the fabric. The more needles, the tighter the fabric will usually be, and the more delicate the feel will be; while fabrics with fewer needles may be more breathable and suitable for summer clothing needs. Secondly, different knitting machine models will also have a significant impact on the characteristics of the fabric. Modern knitting machines usually have higher precision and efficiency, and can produce more complex patterns and designs to meet the market's demand for personalization and diversification.
In addition, the choice of knitting method is equally important. Common knitting methods include flat needles, ribbed needles, loop needles, etc., each of which gives the fabric different elasticity and appearance effects. For example, ribbed knitted fabrics usually have good elasticity and recovery due to their unique structure, which is suitable for making close-fitting clothing. Loop needles are often used to make heavier fabrics, suitable for winter clothing.
After weaving, the fabric is not the final product, but needs to go through a series of subsequent processing techniques, such as immersion, dyeing, etc. These processes can not only enhance the color saturation and visual effect of the fabric, but also improve the durability and comfort of the fabric. The immersion process can remove impurities in the fabric and ensure the purity of the fabric, while the dyeing process adds rich colors to the fabric, making it more competitive in the market.
3.Dyeing and processing
The dyeing process of knitted fabrics is a relatively complex and technically demanding process, involving comprehensive consideration of multiple factors. First of all, the choice of dyeing must be based on different fabric materials. For example, cotton knitted fabrics are usually suitable for direct dyes, while natural fibers such as wool or silk are more suitable for acid dyes. This is because different dyes have different affinities with fibers, and choosing the right dye can ensure the best presentation of the dyeing effect.
Common dyeing methods include melt dyeing and direct dyeing. Melt dyeing is usually suitable for synthetic fibers, such as polyester fibers. This method heats the dye to a molten state and allows it to penetrate into the fiber to achieve a uniform dyeing effect. Direct dyeing is to apply the dye directly to the fiber surface. It is suitable for some natural fibers and can be dyed at a lower temperature, saving energy.
Dyeing processing is not only to enhance the appearance of the fabric, but also has an important impact on the color, color fastness and gloss of the finished product. Color fastness refers to the ability of the dyed fabric to maintain its color under external environments such as washing, friction and light. Good color fastness can ensure the durability and beauty of the fabric during use. In addition, the glossiness during the dyeing process will also affect the overall visual effect of the fabric. Fabrics with strong gloss usually appear more upscale and attractive.
In dyeing processing, the choice of dyes is crucial. Generally speaking, the dyes commonly used in dyeing processing include melt dyes, direct dyes and acid dyes. Melt dyes are suitable for synthetic fibers and can provide bright colors; direct dyes are suitable for cotton fabrics and have good color performance; while acid dyes are mainly used for wool and silk, which can give the fabric rich colors and gloss. The specific dye selection needs to be comprehensively considered based on the material of the fabric, the use environment and the positioning of the final product.
4.Tidy and processing
After dyeing, the fabric enters the finishing process, which is an important step to ensure that the fabric achieves the best finished product effect. The finishing process usually includes multiple links, such as sizing, rolling, drying and calendering, each of which plays a vital role in the final quality and appearance of the fabric.
First of all, sizing is the first step in finishing, and the main purpose is to enhance the rigidity and gloss of the fabric by adding sizing. The selection and amount of sizing will directly affect the feel and appearance of the fabric. Proper sizing can make the fabric more stiff, reduce wrinkles, and enhance the overall visual effect.
Next is the rolling process, which is mainly to roll up the fabric neatly for subsequent storage and transportation. During the rolling process, the operator needs to ensure the flatness of the fabric, avoid wrinkles and deformation, so as to keep the fabric neat and beautiful.
Drying is an indispensable step in finishing, the purpose of which is to remove moisture from the fabric and ensure its stability and durability in subsequent use. The drying temperature and time need to be adjusted according to the material of the fabric to prevent excessive temperature from causing shrinkage or damage to the fabric.
Finally, calendering is the process of flattening the fabric through mechanical equipment to improve its gloss and feel. Calendering not only makes the surface of the fabric smoother, but also enhances its visual appeal, making the finished fabric look more upscale.
5.Finished product processing
Finally, after finishing the knitted fabric, it enters the finished product processing stage, which is a key link to improve the overall texture and quality of the fabric. Finished product processing mainly includes special processing techniques such as printing and hot stamping, which can not only add visual appeal to the fabric, but also enhance its market competitiveness.
First of all, finishing is an important part of finished product processing, mainly involving the shaping and calendering of the fabric. Through this process, the surface of the fabric will become smoother, and the wrinkles and irregular edges will be trimmed, making it more neat and professional in appearance. Calendering can significantly improve the gloss of the fabric, making it look more upscale and enhancing consumers' desire to buy.
Printing is a special process commonly used in the finished product processing of knitted fabrics. Through printing, various patterns and colors can be added to the fabric to make it more vivid and full of personality. Printing technology has many forms, including screen printing, digital printing and thermal transfer, each of which has its own unique effects and scope of application. Printing can not only enhance the aesthetics of the fabric, but also meet the market's demand for personalization and diversification, attracting more consumers' attention.
Hot stamping is a processing method that can add a sense of luxury to the fabric. By applying metal foil or special coating on the surface of fabric, hot stamping can create a shiny effect, giving the fabric a unique luster under light. This process is often used in high-end clothing and fashion accessories, which can significantly enhance the added value and market positioning of products.
In addition, the finished product processing may also include other special treatments, such as waterproof, anti-wrinkle, antibacterial and other functional processing, which can further enhance the practicality and comfort of the fabric and meet the needs of different consumers.
After completing the above five steps, we usually conduct rolling inspection of our fabrics to ensure that the quantity meets customer requirements. This process is not just a simple quantity check, but also includes a comprehensive inspection of the quality of the fabric. We will carefully observe the color, texture, thickness, etc. of the fabric to ensure that each roll of fabric meets our standards and customer expectations. In addition, some customers will require more stringent testing of our fabrics. These tests may include physical performance testing, chemical composition analysis, and durability evaluation. In order to meet the needs of our customers, we usually cooperate with professional testing agencies to ensure that the fabrics meet industry standards in all aspects. This not only enhances customers' trust in our products, but also provides strong support for our competitiveness in the market. It plays a vital role in establishing a good brand image and winning the favor of more customers.
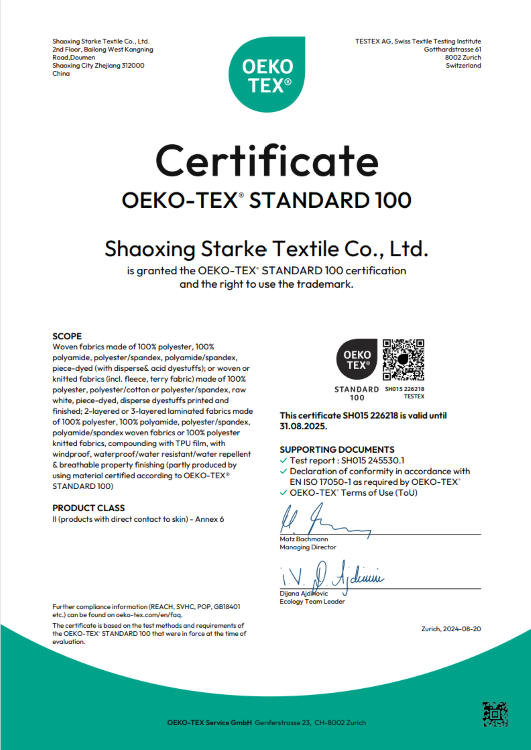
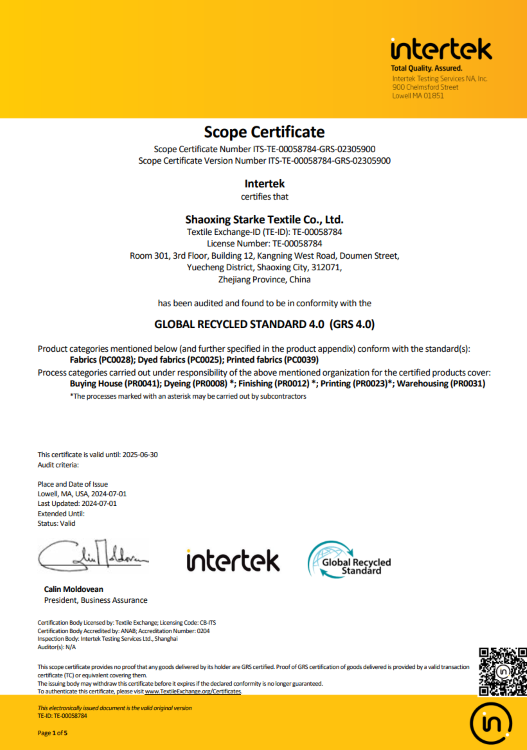